Everything about Sacramento Warehouse
Wiki Article
The Basic Principles Of Sacramento Crossdock
Table of ContentsThe 2-Minute Rule for Sacramento CrossdockSome Known Questions About Sacramento Cross Dock.Crossdock Warehouse Fundamentals ExplainedSacramento Crossdock Warehousing for BeginnersThe Ultimate Guide To Sacramento Cross Dock
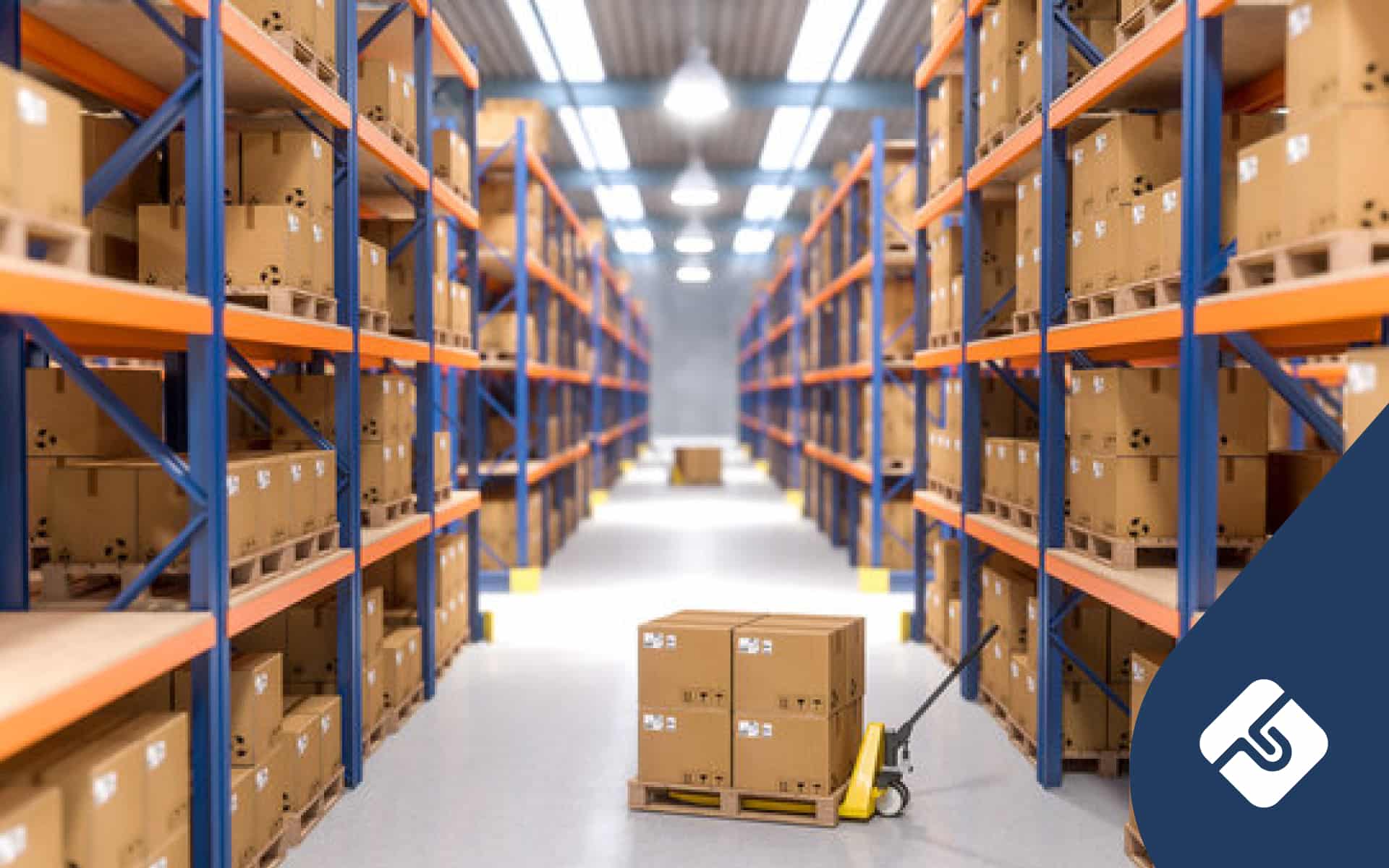
As a component of SCM, effective inventory management might lead to a stronger supply chain. An additional reason great warehousing is necessary to SCM is that it supplies a method for organizations to make certain the accessibility of the ideal products at the appropriate place whenever the time is. It increases the utility worth of the items this way - Sacramento Crossdock.
Of course, they become much more reluctant when uncertainty exists around the prompt distribution of products. Nowadays, shipment speed seems to be one of the substantial variables that customers take into consideration when picking an item as well as deciding whether or not to continue with the acquisition.
An Unbiased View of Sacramento Crossdock Warehousing
A substantial factor to purchase developing a storehouse is the lots of well-known financial benefits that include it. Not just the enhanced efficiency of the supply chain however additionally the warehouse's storage ability and also exactly how it functions as a main place for your products add to its economic advantages.These points can be seen or know with debt consolidation and accumulation operations. Below's a more detailed take a look at just how consolidation and accumulation might aid lower prices: With debt consolidation operations, there's no demand to deliver items independently from several sources because they can be supplied to your stockroom as supplies. When an order is placed, you or your team can load and also deliver the item out from there.
Not only that, yet great warehousing also boosts client service and supplies financial benefits. Every one of these things could result in higher revenue and also enhanced company earnings.
About Sacramento Warehouse
Delivering materials for order fulfillment. Individuals who pack items right into a storage facility as well as others ("pickers") that fill orders in a true warehouse, plus those that take care of the center and operation. Security to secure saved items. Access to economical transport to bring products in or move them out as orders are satisfied.They likewise need to make certain that items are kept in a risk-free as well as safe fashion. In retail shops, products are kept and also arranged in a stockroom and delivered to consumers or other shops.
Putaway is the procedure of physically, as well as methodically, putting products right into their proper last storage places. Staff picks Item to putaway from Putaway Staging location, Generally Pallets or Carts with Item all set to be putaway, Using RF Scanner, determine what cart/pallet/job you are putting away and check unique identifier to begin Putaway, Picker takes a trip to area to place item for storage, Ideal best in course systems tell staff where to place item, but several stockrooms still have staff area product where they understand there is empty space (with some requirements used)RF Check Product being putaway and also Location where the Product is putaway, Continue procedure (go to location and also place supply) up until entire order, pallet, cart, etc is complete Weight and also measurements of product/pallet being putaway, Stowability of Product (ie fragile, stackable, and so on)Transaction quantity (HOT items placed close vs NOT far away)Amount received, Value of item, Pick Type of Product (solitary choice, batch pick, collection choice, zone pick, and so on) Accurate Putaway is imperative in the stockroom operation, making certain that Product can be conveniently located specifically when it is needed.
The Of Crossdock Warehouse
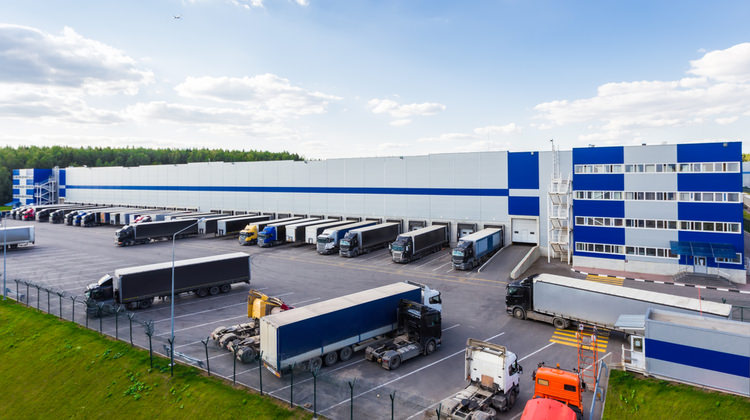
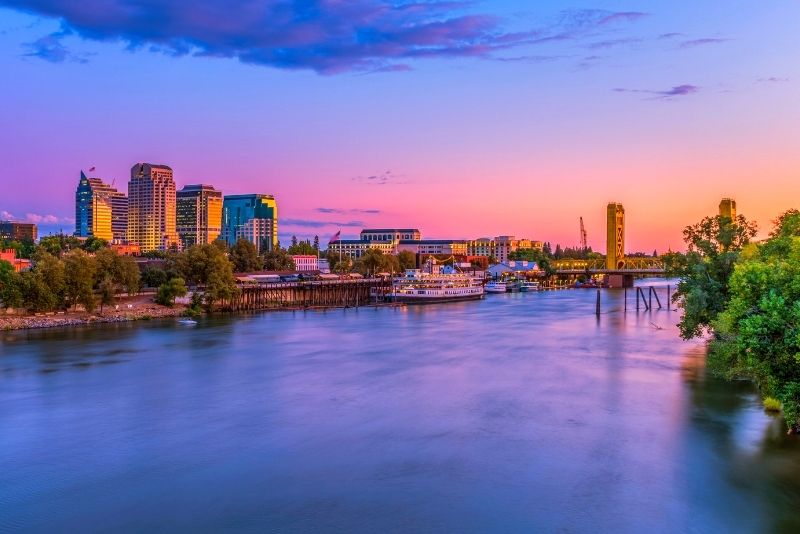
Comparable to exactly how Getting lays the structure for an accurate stock, Selecting lays the structure to accurately satisfy a customer's order. Choosing is the procedure of celebration Products to meet a client's order request. Picker is assigned Select(s)There are numerous select approaches, each operation is distinct in what is most effective for their requirements, Zone choosing, batch picking, solitary order picking, wave selecting, as well as extra, Utilizing RF Scanner, or comparable, start selecting by entering the Unique Choose Identifier (set #, Order #, SO #, Select #, other recommendation)Picker is directed with click resources the Choose Course (ideally based upon optimization logic) to accomplish the Choose, scanning Products and Locations as they advance, Chosen products might be put in totes, pallets, carts, rack, etc throughout choice, Fully chose orders supplied to next phase of procedure, Picked orders might be provided to a Quality assurance location, Packing/Shipping area, or directly to outbound staging (if choice to label procedure) relying on operation Limitations/abilities of current Storage facility Monitoring System (WMS)Volume of Orders # of Product Lines per Order, Kind of storage space media (shelving vs racking vs ground pallet storage space)What the Packaging and also Delivery Refine looks like (carefully intertwined to Selecting)Product need extra attention during packaging? Transportation Administration System (TMS) with the ability of providing delivery tags prior to items are picked? A lot more! Storage facility Format Selecting have to be done properly, with quality assurance measures in position post-picking, to attain customer order gratification precision near 100%.
If during shipping the weight is not within the defined tolerance range, after that the customer will be motivated to take activity, Measurement tolerance check during Delivery, Similar to Weight tolerance based on system dimension information Packing and Delivery is a significant focus of warehouses, as it usually comes to be a traffic jam since Order Handling Time have to be as brief as feasible to satisfy client assumptions.
Do NOT sacrifice top quality! It is necessary to keep in mind, relying on the storage facility operation Packing might be integrated with the Selecting process. Inventory Control is an essential part of all stockroom operations. You can guarantee the supply at the stockroom is accurate and up-to-date with a well defined Stock Control process.
Getting My Sacramento Crossdock To Work
Cycle Counts and also Complete Stock Counts you could try these out are tools connected with preserving Stock Control. Cycle Counts take place continually while regular procedures proceed, however Full Supply Counts take place periodically and also call for all product movement to stop up until a full exact count is completed. Closure all stock movements, completing all Product Activities in the Storehouse (physically as well as methodically)Make certain all incoming as well as additional reading outgoing orders that have been physically refined, have additionally been processed in WMSBreak storage facility team right into teams to matter (occasionally 1 individual team all right)Groups are designated locations to count Assign small-medium areas to count, after that groups sign in for more areas as needed, Teams count assigned locations, tape-recording counts of item per area, Teams often utilizing RF Scanners to videotape counts, Or else need to do paper-based which is tough to accomplish a Blind Count, Team reports back as soon as completed and receive next Matter Assignment, After areas are Counted, the Manager/Lead evaluates all Variances, Manager designates DIFFERENT Team to state the distressed Products and/or Locations, If 2nd team counts same as 1st group, make inventory adjustment to match physical matter.Report this wiki page